第一章 金属材料的力学性能测试
实验一 低碳钢和铸铁的拉伸实验
一、 实验目的
1. 测定低碳钢的弹性模量E、屈服极限σs、强度极限σb、延伸率δ和断面收缩率Ψ。
2. 测定铸铁的强度极限σb。
3. 观察低碳钢拉伸过程中的弹性、屈服、强化、颈缩、断裂等物理现象。
4. 熟悉材料实验机和其它仪器的使用。
5.比较低碳钢和铸铁压缩变形和破坏现象。
6.测定低碳钢的屈服极限σs和铸铁的强度极限σb。
7.比较铸铁在拉伸和压缩两种受力形式下的机械性能、分析其破坏原因。
8.熟悉压力实验机的使用方法。
二、 实验设备
1. 2000kN液压式压力试验机,WE-600型万能材料试验机,WDW-100型微机控制电子万能试验机。
2. 游标卡尺。
3. 引伸仪。
三、 试件介绍
1、拉伸实验试件
由于试件的形状和尺寸对实验结果有一定的影响,为便于互相比较,应按统一规定加工成标准试件。按国家有关标准的规定,拉伸试件分为比例试件和非比例试件两种。在试件中部,用来测量试件伸长的长度,称为原始标距(简称标距)。比例试件的标距l0与原始横截面面积A0的关系规定为
(1.1)
式中系数k的取值为5.65时为短试件,取11.3时为长试件。对直径为d0的圆截面试件,短试件和长试件的标距l0分别为5 d0和10 d0。非比例试件的l0和A0不受上述关系限制。本实验采用圆截面的短试件,即l0=5 d0。
2、压缩实验试件
根据国家有关标准,低碳钢和铸铁等金属材料的压缩试件一般制成圆柱形试件。低碳钢压缩试件的高度和直径的比例为3:2,铸铁压缩试件的高度和直径的比例为2:1。试件均为圆柱体。
四、实验原理及方法
I、拉伸实验部分
常温下的拉伸实验可以测定材料的弹性模量E、屈服极限
、强度极限
、延伸率
和断面收缩率
等力学性能指标,这些参数都是工程设计的重要依据。
1.低碳钢弹性模量E的测定
由材料力学可知,弹性模量是材料在弹性变形范围内应力与应变的比值,即
(1.2)
式中:E—材料的弹性模量;
应力;
应变。
因为
,
,所以弹性模量E又可以表示为:
(1.3)
式中: P—实验时所施加的荷载;
A-以试件直径的平均值计算的横截面面积;
L0—引伸仪标距;
试件在载荷P作用下,标距L0段的伸长量。
在弹性变形范围内,对试件作用拉力P,并量出拉力P引起的标距内伸长
,即可求得弹性模量E。实验时,拉力P值由试验机读数盘示出,试件标距L0=50㎜(不同的引伸仪标距不同),试件横截面面积A可算出,只要测出标距段的伸长量
,就可得到弹性模量E。
在弹性变形阶段内试件的变形很小,标距段的变形(伸长量
)需用放大倍数为200倍的球铰式引伸仪来测量。为检验荷载与变形之间的关系是否符合胡克定律,并减少测量误差,实验时一般用等增量法加载,即把载荷分成若干个等级,每次增加相同的载荷
,逐级加载。为保证应力不超过弹性范围,以屈服载荷的70%~80%作为测定弹性模量的最高载荷Pn。此外,为使试验机夹紧试件,消除试验机机构的间隙等因素的影响,对试件应施加一个初始载荷P0(本实验中P0=2.0kN)。
实验时,从P0到Pn逐级加载,载荷的每级增量均为
。对应每级载荷Pi,记录相应的伸长
,
与
之差即为变形增量
,它是
引起的变形(伸长)增量。在逐级加载中,如果得到的
基本相等,则表明
与P为线性关系,符合胡克定理。完成一次加载过程,将得到
的一组数据,按平均法计算弹性模量,即
(1.4)
其中,
为变形增量的平均值;200为测量变形时的放大系数。
2.屈服极限
、强度极限
的测定
测定弹性模量后继续加载使材料达到屈服阶段,进入屈服阶段时,载荷常有上下波动,其中较大的载荷称上屈服点,较小的称下屈服点。一般用第一个波峰的下屈服点表示材料的屈服载荷
,它所对应的应力即为屈服极限
。
屈服阶段过后,材料进入强化阶段,试件又恢复了承载能力。载荷达到最大值
时,试件某一局部的截面明显缩小,出现“颈缩”现象。这时示力盘的从动针停留在
位置,主动针迅速倒退,表明荷载迅速下降,试件即将被拉断。这时从动针所示的载荷即为破坏载荷
,所对应的应力叫强度极限
。
3.延伸率
和断面收缩率
的测定
试件的原始标距为
,拉断后将两段试件紧密对接在一起,量出拉断后的标距长
,延伸率应为
(1.5)
式中
—试件原始标距;
—试件拉断后标距长度。
对于塑性材料,断裂前变形集中在紧缩处,该部分变形最大,距离断口位置越远,变形越小,即断裂位置对延伸率是有影响的。为了便于比较,规定断口在标距中央三分之一范围内测出的延伸率为测量标准。如断口不在此范围内,则需进行折算,也称断口移中。具体方法如下:以断口O为起点,在长度上取基本等于短段格数得到B点,当长段所剩格数为偶数时(见图1.1b),则由所剩格数的一半得到C点,取BC段长度将其移至短段边,则得断口移中得标距长,其计算式为

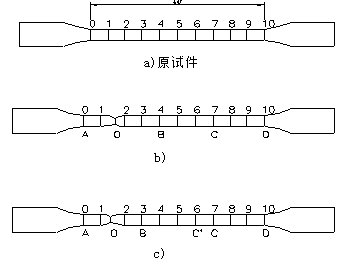
图1.1标距长度示意图
如果长段取B点后所剩格数为奇数(见图1.1c),则取所剩格数加一格之半得C1点和减一格之半得C点,移中后标距长为
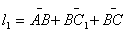
将计算所得的
代入式中,可求得折算后的延伸率
。
为了测定低碳钢的断面收缩率,试件拉断后,在断口处两端沿互相垂直的方向各测一次直径,取平均值
计算断口处横截面面积,再按式(1.6)计算面积收缩。
(1.6)
式中: A0—试件原始横截面面积;
A1—试件拉断后断口处最小面积。
II、压缩实验部分
压缩实验是研究材料性能常用的实验方法。对铸铁、铸造合金、建筑材料等脆性材料尤为合适。通过压缩实验观察材料的变形过程、破坏形式,并与拉伸实验进行比较,可以分析不同应力状态对材料强度、塑性的影响,从而对材料的机械性能有比较全面的认识。
压缩试验在压力试验机上进行。当试件受压时,其上下两端面与试验机支撑之间产生很大的摩擦力,使试件两端的横向变形受到阻碍,故压缩后试件呈鼓形。摩擦力的存在会影响试件的抗压能力甚至破坏形式。为了尽量减少摩擦力的影响,实验时试件两端必须保证平行,并与轴线垂直,使试件受轴向压力。另外。端面加工应有较高的光洁度。
低碳钢压缩时也会发生屈服,但并不象拉伸那样有明显的屈服阶段。因此,在测定Ps时要特别注意观察。在缓慢均匀加载下,测力指针等速转动,当材料发生屈服时,测力指针转动将减慢,甚至倒退。这时对应的载荷即为屈服载荷Ps。屈服之后加载到试件产生明显变形即停止加载。这是因为低碳钢受压时变形较大而不破裂,因此愈压愈扁。横截面增大时,其实际应力不随外载荷增加而增加,故不可能得到最大载荷Pb,因此也得不到强度极限σb,所以在实验中是以变形来控制加载的。
铸铁试件压缩时,在达到最大载荷Pb前出现较明显的变形然后破裂,此时试验机测力指针迅速倒退,从动针读取最大载荷Pb值,铸铁试件最后略呈故形,断裂面与试件轴线大约呈45°。
五、实验步骤
I、拉伸实验部分
1.试验机准备。根据估算的最大载荷,选择合适的示力度盘(量程)和相应的摆锤,并按相应的操作规程进行操作。
2.测量试件的直径。在标距两端及中部三个位置上,沿互相垂直的方向,测量试件直径,以其平均值计算弹性模量,以其最小值计算强度和断面收缩率。
3.安装试件。
4.安装引伸仪(只用于低碳钢拉伸试验)
5.进行预拉(只用于低碳钢拉伸试验)。为了检查机器和仪表是否处于正常状态,先把荷载预加到略小于Pn(测定弹性模量E时最大荷载),然后卸载到0~P0之间。
6.加载。在测定低碳钢的弹性模量时,先加载至P0,调整引伸仪读数为零或记录初始读数。加载按等增量法进行,记录每级荷载下的引伸仪读数,载荷最大加至Pn,然后取下引伸仪。加载应保持匀速、缓慢。测出屈服载荷Ps后,可稍加实验速率,最后直到将试件拉断,记录最大载荷Pb。对铸铁试件,应缓慢匀速加载,直至试件被拉断,记录最大载荷Pb。
7.取下试件,将试验机恢复原状。观察试件并测量有关数据。
II、压缩实验部分
1.试验机准备。根据估算的最大载荷,选择合适的示力度盘(量程)和相应的摆锤,并按相应的操作规程进行操作。
2.测量试件的直径和高度。测量试件两端及中部三处的截面直径,取三处中最小一处的平均直径计算横截面面积。
3.将试件放在试验机活动台球形支撑板中心处。
4.开动试验机,使活动台上升,对试件进行缓慢均匀加载。对于低碳钢,要及时记录其屈服载荷,超过屈服载荷后,继续加载,将试件压成鼓形即可停止加载。铸铁试件加压至试件破坏为止,记录最大载荷。
5.取出试件,将试验机恢复原状,观察试件。
六、实验结果的处理
I、拉伸实验部分
1.计算屈服极限
和强度极限
,
(1.7)
其中
,
为最小直径。
2.计算低碳钢的弹性模量E
(1.8)
其中:
为载荷增量,
,为变形增量的平均值;
,d为平均直径。
3.计算延伸率
和断面收缩率
(1.9)
(1.10)
II、压缩实验部分
1.计算低碳钢的屈服极限
(1.11)
2.计算铸铁的强度极限
(1.12)
其中
,
为试件实验前最小直径
七、思考题
1.参考低碳钢拉伸图,分段回答力与变形的关系以及在实验中反映出的现象。
2.由低碳钢、铸铁的拉伸图和试件断口形状及其测试结果,回答二者机械性能有什么不同。
3.测定E时为何要加初载荷P0并限制最高载荷Pn?使用分级加载的目的是什么?
4.实验时如何观察低碳钢的屈服极限?
5.为何低碳钢压缩测不出破坏载荷,而铸铁压缩测不出屈服载荷?
6.为什么铸铁压缩时沿轴线大致成45°方向的斜截面破坏?
7.通过拉伸与压缩实验,比较低碳钢的屈服极限在拉伸和压缩时的差别?
8.通过拉伸与压缩实验,比较铸铁的强度极限在拉伸和压缩时的差别?
根据国家有关标准,低碳钢和铸铁等金属材料的压缩试件一般制成圆柱形试件。低碳钢压缩试件的高度和直径的比例为3:2,铸铁压缩试件的高度和直径的比例为2:1。试件均为圆柱体。
实验二 扭转试验
一、实验目的
1.测定低碳钢的剪切屈服极限
及剪切强度极限
。
2.测定铸铁的剪切强度极限
。
3.观察并比较低碳钢及铸铁试件扭转破坏的情况。
二、实验设备和量具
1.0.02mm游标卡尺。
2.扭转材料实验机。
三、试件制作
金属的扭转试件采用标准的圆试件。标矩部分直径d0=10
0.1mm,标矩L0=100mm或50mm,如图3-3所示。具体要求可参考标准YB36-64。
四、实验步骤
1.测量试件尺寸。取三个截面互垂方向测两次,取平均值。用三处截面中平均值最小者计算WP。
2.根据试件的负荷水平选择力盘。
3.安装绘图纸、调节机器零点。
4.安装试件。沿试件表面画一母线以定性观察变形现象。
5.扭转角度盘调零。
6.开机实验。为了便于观察和记录数据,初始阶段应尽量采用慢速或手摇加载。加载必须均匀、缓慢、不得停顿。材料屈服时及时记录Ms。材料强化后可考虑改变加载速度,直至断裂,并记录最大扭矩Mb。
7.试件断裂后立即停机。取下试件观察分析断口及塑性变形能力。
五、结果整理
1.强度指标计算。
2.画出两种材料的扭转曲线及断口形貌草图。分析破坏原因。
3.分析、比较铸铁拉、压、扭三种受力形式下的机械性能。报告规格和要求可参考拉伸试验。
六、思考题
1、低碳钢拉伸和扭转的断裂方式是否一样?破坏原因是否相同?
2、铸铁在压缩和扭转时,断口都与轴线成45o,破坏原因是否相同?
第二章 材料力学电测综合实验
实验三 纯弯曲梁的正应力实验
一、实验目的
1. 测定梁在纯弯曲时横截面上正应力大小和分布规律
2. 验证纯弯曲梁的正应力计算公式
二、实验仪器设备和工具
3. 组合实验台中纯弯曲梁实验装置
4. 力&应变综合参数测试仪
5. 游标卡尺、钢板尺
三、实验原理及方法
在纯弯曲条件下,根据平面假设和纵向纤维间无挤压的假设,可得到梁横截面上任一点的正应力,计算公式为
(2.1)
式中:M—弯矩;
Iz—横截面对中性轴的惯性矩;
y—所求应力点至中性轴的距离。
为了测量梁在纯弯曲时横截面上正应力的分布规律,在梁的纯弯曲段沿梁侧面不同高度,平行于轴线贴有应变片(如图2-1)。
△ P/2 △ P/2

















h














a a b

L
图 2-1 应变片在梁中的位置
实验可采用半桥单臂、公共补偿、多点测量方法。加载采用增量法,即每增加等量的载荷△P,测出各点的应变增量△ε,然后分别取各点应变增量的平均值△ε实i,依次求出各点的应变增量
σ实i=E△ε实i (2.2)
将实测应力值与理论应力值进行比较,以验证弯曲正应力公式。
四、实验步骤
1. 设计好本实验所需的各类数据表格。
2. 测量矩形截面梁的宽度b和高度h、载荷作用点到梁支点距离a及各应变片到中性层的距离yi。
3. 拟订加载方案。先选取适当的初载荷P0(一般取P0 =10%Pmax左右),估算Pmax(该实验载荷范围Pmax≤4000N),分4~6级加载。
4. 根据加载方案,调整好实验加载装置。
5. 按实验要求接好线,调整好仪器,检查整个测试系统是否处于正常工作状态。
6. 加载。均匀缓慢加载至初载荷P0,记下各点应变的初始读数;然后分级等增量加载,每增加一级载荷,依次记录各点电阻应变片的应变值εi,直到最终载荷。实验至少重复两次。
7. 作完实验后,卸掉载荷,关闭电源,整理好所用仪器设备,清理实验现场,将所用仪器设备复原,实验资料交指导教师检查签字。
五、实验结果处理
1. 实验值计算
根据测得的各点应变值εi求出应变增量平均值△εi,代入胡克定律计算
各点的实验应力值,因1µε=10-6ε,所以各点实验应力计算
σi实=Eεi实=E×△εi×10-6 (2.3)
2. 理论值计算
载荷增量 △P= 500N
弯距增量 △M=△P×a/2=31.25 N·m
各点理论值计算
(2.4)
3. 绘出实验应力值和理论应力值的分布图
分别以横坐标轴表示各测点的应力σi实和σi理,以纵坐标轴表示各测
点距梁中性层位置yi,选用合适的比例绘出应力分布图。
4. 实验值与理论值的比较
六、思考题
1. 影响实验结果准确性的主要因素是什么?
2. 根据实验结果解释梁弯曲时横截面上正应力分布规律。
3. 实验时没有考虑梁的自重,会引起误差吗?为什么?
4. 梁弯曲的正应力公式并未涉及材料的弹性模量E,而实测应力值的计算却用上了弹性模量E,为什么?
实验四 材料弹性模量E和泊松比µ的测定
一、实验目的
1. 测定常用金属材料的弹性模量E和泊松比µ。
2. 验证胡克(Hooke)定律。
二、实验仪器设备和工具
1. 组合实验台中拉伸装置
2. 力&应变综合参数测试仪
3. 游标卡尺、钢板尺
三、实验原理和方法
















试件采用矩形截面试件,电阻应变片布片方式如图2-4。在试件中央截面上,沿前后两面的轴线方向分别对称的贴一对轴向应变片R1、R1ˊ和一对横向应变片R2、R2ˊ,以测量轴向应变ε和横向应变εˊ。

P P

R1 R1ˊ R1 R R



R2 R2ˊ R2




b h

补偿块

P P
图 2-4 拉伸试件及布片图
1. 弹性模量E的测定
由于实验装置和安装初始状态的不稳定性,拉伸曲线的初始阶段往往
是非线性的。为了尽可能减小测量误差,实验宜从一初载荷P0(P0≠0)开始,采用增量法,分级加载,分别测量在各相同载荷增量△P作用下,产生的应变增量△ε,并求出△ε的平均值。设试件初始横截面面积为A0,又因ε=△l/l,则有
(2.25)
上式即为增量法测E的计算公式。
式中 A0 — 试件截面面积
△ε — 轴向应变增量的平均值
用上述板试件测E时,合理地选择组桥方式可有效地提高测试灵敏度和实验效率。下面讨论几种常见的组桥方式。
(1)单臂测量(图2-5a)

实验时,在一定载荷条件下,分别对前、后两枚轴向应变片进行单片测量,并取其平均值ε=(ε1+ε1′)/2。显然(εn+ε0)代表载荷(Pn+P0)作用下试件的实际应变量。而且ε消除了偏心弯曲引起的测量误差。
(2)轴向应变片串连后的单臂测量(图2-5b)
为消除偏心弯曲引起的影响,可将前后两轴向应变片串联后接在同一桥臂(AB)上,而邻臂(BC)接相同阻值的补偿片。受拉时两枚轴向应变片的电阻变化分别为
△R1 + △RM
△R1′-△RM
△RM为偏心弯曲引起的电阻变化,拉、压两侧大小相等方向相反。根据桥路原理,AB桥臂有
△R/R=(△R1+△RM +△R1′-△RM)/(R1 + R1′)=△R1/△R1
因此轴向应变片串联后,偏心弯曲的影响自动消除,而应变仪的读数就等于试件的应变即εp =εd,很显然这种测量方法没有提高测量灵敏度。

B

R1 R




工作片 Uab





A C



补偿片
R3 R4
机内电阻 D
E


(a)



B B




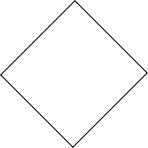
R1′ R R1′ R2

R1 R R1 R2′

Uab Uab





A C A C



R3 R4 R3 R4

D D
E E



(b) (c)



B B
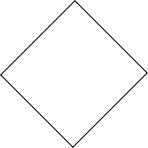
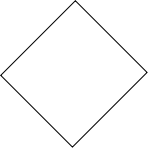
R1 R R1 R2


Uab Uab





A C A C



R R1′ R2′ R1′

D D
E E



(d) (e)
图2-5 几种不同的组桥方式
(3)串联后的半桥测量(图2-5c)
将两轴向应变片串联后接AB桥臂;两横向应变片串联后接BC桥臂,偏心弯曲的影响可自动消除,而温度影响也可自动补偿。根据桥路原理
εd=ε1-ε2-ε3+ε4
其中ε1=εp;ε2=-μεp, εp代表轴向应变,μ为材料的泊松比。由于
ε3、ε4 为零,故电阻应变仪的读数应为
εd=εp(1+μ)
有 εp=εd/(1+μ)
如果材料的泊松比已知,这种组桥方式使测量灵敏度提高(1+μ)倍。
(4)相对桥臂测量(图2-5d)
将两轴向应变片分别接在电桥的相对两臂(AB、CD),两温度补偿片接在相对桥臂(BC、DA),偏心弯曲的影响可自动消除。根据桥路原理
εd=2εp
测量灵敏度提高2倍。
(5)全桥测量
按图2-5(e)的方式组桥进行全桥测量,不仅消除偏心和温度的影响,而且测量灵敏度比单臂测量时提高2(1+μ)倍,即
εd=2εp(1+μ)
2. 泊松比μ的测定
利用试件上的横向应变片和纵向应变片合理组桥,为了尽可能减小测量误差,实验宜从一初载荷P0(P0≠0)开始,采用增量法,分级加载,分别测量在各相同载荷增量△P作用下,横向应变增量△εˊ和纵向应变增量△ε。求出平均值,按定义

便可求得泊松比μ。
四、实验步骤
1. 设计好本实验所需的各类数据表格。
2. 测量试件尺寸。在试件标距范围内,测量试件三个横截面尺寸,取三处横截面面积的平均值作为试件的横截面面积A0。见附表1
3. 拟订加载方案。先选取适当的初载荷P0(一般取P0 =10% Pmax左右),估算Pmax(该实验载荷范围Pmax≤5000N),分4~6级加载。
4. 根据加载方案,调整好实验加载装置。
5. 按实验要求接好线(为提高测试精度建议采用图3-5d所示相对桥臂测量方法),调整好仪器,检查整个测试系统是否处于正常工作状态。
6. 加载。均匀缓慢加载至初载荷P0,记下各点应变的初始读数;然后分级等增量加载,每增加一级载荷,依次记录各点电阻应变片的应变值,直到最终载荷。实验至少重复两次。实验报告中半桥单臂测量数据表格,其他组桥方式实验表格可根据实际情况自行设计。
7. 作完实验后,卸掉载荷,关闭电源,整理好所用仪器设备,清理实验现场,将所用仪器设备复原,实验资料交指导教师检查签字。
五、实验结果处理
1. 弹性模量计算


E = =
2. 泊松比计算




μ= =
六、思考题
1. 分析纵、横向应变片粘贴不准,对测试结果的影响。
2. 根据实验测得的E实、μ实值与已知E理、μ理值作对比,分析误差原因。
3. 采用什么措施可消除偏心弯曲的影响?
附录A 液压式万能试验机
液压式万能试验机广泛应用于材料试验中,其结构原理可分为四大部分。液压万能试验机的外形如图A-1,结构原理如图A-2所示。
一、加力部分
在液压万能试验机的机座上装有两根固定立柱,主要由这两根立柱支承大横梁、小横梁、大活塞和工作台。当开动电动机时,传动皮带就带动油泵工作,高压油液经油管进油阀输送到工作油缸,推动大活塞往上运动。小横梁固定在大活塞顶上,活塞上升时,通过两根活动立柱带动工作台往上运行。做拉伸实验时,将拉伸试件的两端夹于上拉伸夹头和下拉伸夹头(固定不动)之间,当工作台上升时,使试件发生拉伸变形;做压缩实验时,把压缩试件放在下压头中心位置处,当工作台上升时使上压头接触试件后,产生压缩变形;做弯曲实验时,把弯曲试件放在两支座上,当工作台上升时使上压头接触试件后,产生弯曲变形。进油阀用来控制输入工作油缸中的油量,以控制试件的变形速度。实验完毕,关闭进油阀,打开回油阀,把工作油缸里的油液泄回油箱,使工作台回到原始位置。
由于试件长度不相同,装卡拉伸试件时,可开动机座旁的电动机,使下拉伸夹头很快地上升或下降,以便装卡拉伸试件。当试件夹紧后,就不能用该电动机加载,否则会烧毁电动机,或发生其他事故:。
二、测力部分
实验时,试件受力的大小可在测力盘上直接读出指示值。试件受力后,工作油缸的油具有一定的压力,压力的大小与试件受力的大小是成比例的。由于工作油缸和测力油缸是联通的,故工作油缸和测力油缸所受的油压是相等的。此油压推动测力活塞和测力拉杆,使推杆和摆锤绕支点转动,推杆推动螺杆运动,使齿轮和测力指针旋转,测力盘所读得的数值即表示试件受力的大小。随着科学技术的发展,近来液压万能试验机上已设置了荷载显示电压表。
油压万能试验机的荷载范围可由摆锤的重量来确定。一般试验机都备有三种砣重作为选择荷载范围用,测力盘上相应有三种荷载刻度。如300kN万能试验机,有60kN、150kN、300kN三种测量范围。
三、绘图部分
液压试验机绘图装置有两种方式,第一种是通过固定在万能试验机上夹头上的拉绳带动绘图滚筒转动,滚筒转动方向为变形坐标,螺杆运动方向为力坐标。第二种方式采用电子自动绘图仪绘图。
四、操作部分
该部分主要由进油阀、回油阀和电器开关等组成。进油阀的作用是将油箱里的油送至工作油缸。进油阀的阀门开得大,表示油送到工作油缸的速度快,也就说明试件受力大,变形快。实验时要严格控制进油阀门的大小,保证荷载盘指针均匀地转动。回油阀的作用可使试件卸载,实验做完后,须打开回油阀门,使工作油缸的油流回油箱。万能试验机的具体操作方法如下:
1.选择荷载范围
实验前,首先根据试件材料能承受的最大荷载,选择相应的砣重,确定荷载的范围(如300kN万能试验机分为:0~60kN,0~150kN,0~300kN)。若在万能试验机上挂上A砣,表示0~60kN范围,挂上A、B砣表示0~150kN范围,挂上A、B、C砣表示0~300kN范围。如直径为10mm的低碳钢拉伸试件,估计其最大承载力为40kN左右,选用0~60kN范围即可,其目的是提高荷载测试精度。
2.荷载调零
开动油泵电机,关闭回油阀,再打开进油阀,向工作油缸送油,使工作平台略上升5~10mm后(消除工作平台的自重)转动螺杆使指针对准测力盘上的零点。
3.拨回被动指针。加载时,主动指针带动被动指针转动,试件破坏后,主动指针返回零位,被动指针停留在原位,所指示值就是试件的最大荷载值。
4.安装调整绘图仪的纸和笔。加载时能自动绘制试件受力与变形的曲线图。
5.安装试件。装卡拉伸试件时,先调整上夹头位置,使拉伸区空间与试件长度相适应。调整上夹头位置时,可开动电动机使上夹头上升或下降。当试件夹紧后,就不允许再用电动机使上夹头上升或下降,以免电动机超负荷而烧毁。
6.加载与卸载。试件安装完毕,即可开启进油阀,逐渐对试件进行加载,加载时要求测力指针匀速平稳地转动。切忌猛开进油阀导致加载速度失控,损坏测力机构。实验完毕,关闭电源开关和进油阀,打开回油阀,使工作油缸的油流回邮箱,工作平台下降到初始位置。
附录B WDW-100型微机控制电子万能试验机
一、概述
WDW-100型微机控制电子万能试验机采用伺服电机及伺服调速系统,先进的芯片集成技术和专业设计的数据采集放大和过程控制系统。适用于各种金属与非金属材料的各项力学性能指标的测试。控制软件能实现自动求取弹性模量、屈服强度、抗拉强度、断裂强度、试样延伸率、断面收缩等常规数据,能自动计算试验过程中任一指定点的力、应力、应变、位移等数据结果。
该机分为减速装置、试验机框架、测量控制系统、试验附具等几部分组成。试验机下部为底座,机座内有伺服调速系统及伺服电机和减速装置。伺服调速系统控制伺服电机通过园弧同步带和减速装置驱动丝杠转动,丝杠上有传动螺母,传动螺母与移动梁固结在一起,丝杠转动,移动梁就上下移动,伺服调速系统通过调节伺服电机的转速就可改变移动梁的移动速度,从而满足试验试验要求的各种速度。测力传感器固定在移动中横梁上,传感器上连接有试样的下夹具,试样的上夹具与固定上横梁的联接座相联接。该机带有位移测量传感器,在试验过程中,移动梁上的负荷传感器测定试验力的大小,位移传感器测量移动量,两者的信号经过滤波放大,由专业设计的数据采集放大和控制系统,同时显示试验力、位移量、变形量等。试验速度由操作者根据试件的实际要求而定。
二、使用与操作
1.开机:打开电源开关,预热15分钟;
2.调整限位:试验机后部有两个小手柄是调节上、下限位开关位置的,可根据需要,松开手柄上下移动,调好限位后拧紧即可。
3.试验操作:按照《试验操作软件说明书》的操作步骤操作。
4.急停开关:试验机下角电源开关旁边的红色大按钮是在试验过程中遇到紧急突发情况时使用:情况排除将急停开关按顺时针旋动,即可复位。
附录C WDW-100型微机控制电子万能试验机拉伸程序使用说明
双击桌面DlTest图标,进入拉伸试验程序,主界面如下:
主界面由菜单、工具栏、参数实时显示框、图形坐标系、试验控制按钮、参数设置等部分组成。
一、菜单的使用
1.文件/新试验,清除当前试验数据,设备初始化,图形清空等,预备新试验开始。
2.文件/打开历史记录,打开打开文件对话框,如下;调入以前的试验数据,并在坐标系里重画试验图形,调入试验结果和其它附加信息。
主界面
打开文件对话框
1.文件/保存数据,打开保存对话框如下,选择目录与文件名,保存当前试验数据。
保存数据对话框
2.文件/退出,退出拉伸试验程序,进入试验向导。
3.参数设置/控制参数,保存。
4.参数设置/保护设置,打开询问口令对话框,如下:输入“DlClass”口令,可获得修改保护设置的权限,保护设置面板如下:可以设置负荷的上、下限,当负荷超过上限或低于下限时,设备保护。变形、位移同理。
询问口令对话框
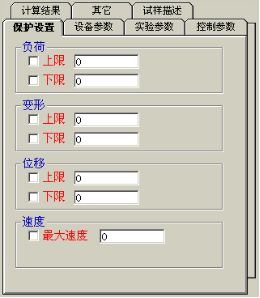
保护设置面板
5.曲线菜单,可以选择各种曲线,包括应力-应变曲线等。
6.实用程序菜单包括计算器、文本编辑器。
二、工具栏的使用
工具栏分上、下两行,上行从左至右,新试验、打开历史记录、保存数据、打印、文本输出、退出,新试验、打开历史记录、保存数据、退出与文件菜单功能相同。“打印”输出试验报告。“文本输出”将当前试验数据以文本文件形式输出。下一行,控制方式可以选择位移控制、负荷控制。试验项目为拉伸试验。横梁控制按钮分上升、下降、停止三个按钮,速度给定条可以改变横梁速度。
三、设置面板的使用
设置面板分为设备参数、实验参数、控制参数、保护参数、试样描述、计算结果、其它和分段试验各类选项。如图:
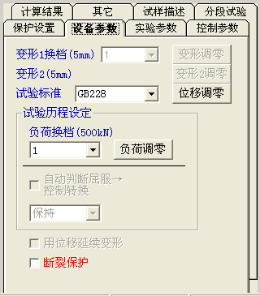
在设备参数设置中,可以改变负荷的档位,负荷分档1,2,5。1倍档量程为0~500kN,2倍档量程为0~250kN,5倍档量程为0~100kN,可以对负荷、位移清零,负荷档位选择要以试样拉断力在倍档量程的30%到80%之间最好。
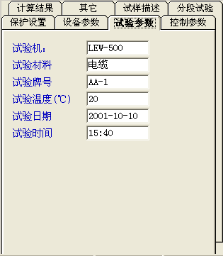
试验参数包括试验机型号、试验材料、试验牌号、试验温度、试验日期、试验时间,试验日期与试验时间无须填写,试验开始时自动填写,其它信息相应填充即可。
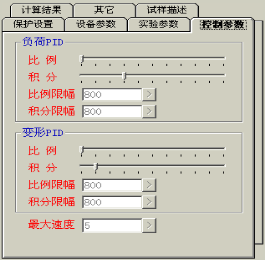
控制参数由设计者保留。
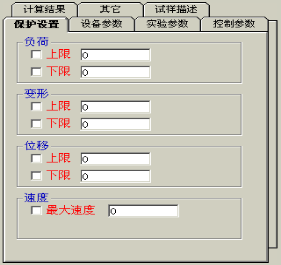
保护设置参看以前说明。
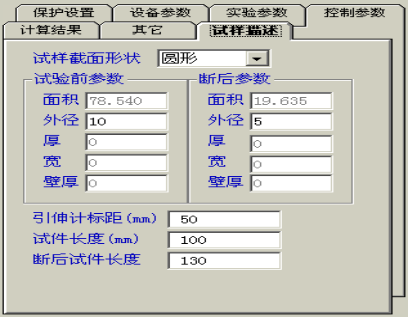
试样描述中,可以选择试样形状、截面尺寸、引伸计标距、试件长度、断后试件长度。试样截面形状可以选择圆形、方形、管形、不规则形,选择圆形,只须输入直径,面积计算机自动算出,方形须输入截面的厚和宽,面积自动算出,管形须输入直径与壁厚,面积自动算出,不规则形直接输入面积。断后参数与试验前参数输入方法一样。引伸计标距不能小于零,试件长度不能小于引伸计标距。
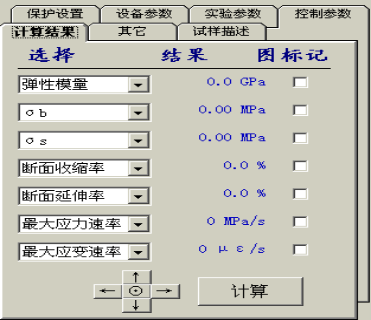
试验结束后,首先保存试验数据。正确输入断后数据,按“计算”按钮,计算机自动处理试验结果,方向箭头放大、缩小图形。⊙使图形恢复原样,在下拉组合框中,可以选择需要的结果,结果在中间的结果框中显示,图标记可以在图形上标出结果的来源,以便验证结果正确性。在应力-应变曲线上,在弹性段的起始点,单击鼠标右键,拉出一条直线到弹性段的终点,松开鼠标右键,可人为改变弹模,其它参数随之改变。
其它部分的设置,保留。
分段试验,如下图。如果段数设置为零,为正常的拉伸试验。在设备参数面板上有一个断裂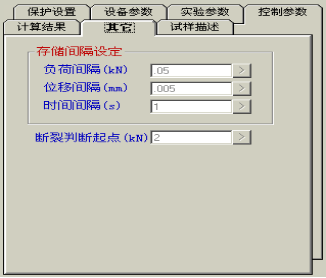
“其它”参数设置对话框
保护选择框,选中断裂保护选择框,当试样被拉断时,程序自动保护停车。在分段试验时,可以选择段数,最大段数为10段,在段数编辑框中填写段数。可以设置每一段的力保持值和保载时间,在试验之前,首先设置试验控制方式和试验速度,设置段数值和各段的力保持值和保载时间和卸载速率。按拉伸按钮,试验按预先设置的试验控制方式和试验速度拉伸试样,当力大于等于第一段的保载值时,进入力控制保载,当第一段保载时间到,继续按预先设置的试验控制方式和试验速度拉伸试样,依次类推。当各段都完成后,按卸载速率卸载。卸载到要求的负荷值,按停止按钮,结束试验。保存试验数据。
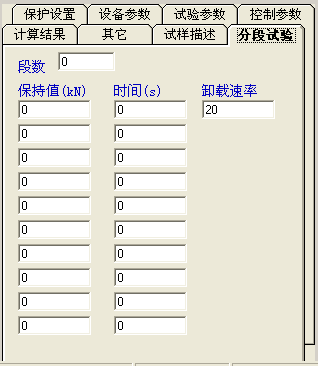
分段试验设置对话框
***在负荷显示上方,双击表头可在负荷与峰值之间切换
四、程序的安装
先安装VB6
将相应设备的目录下的文件夹里DlTest目录复制到c:
对"C:\DlTest\DlTest.exe"创建快捷方式,将快捷方式移动到桌面
双击DlTest快捷方式,既可进入程序
试验操作规程
1.打开逻辑控制单元电源。测控单元电源,计算机电源,运行控制应用程序。电器需预热20分钟。
2.根据需要,可以调整后夹头小车的位置。
※ 注意:在移动小车时,必须把定位小车的定位销拔起,调整完毕,插入定位销,插入定位销后不可再移动小车,否则将损坏电机。
3.启动油泵,把逻辑控制单元的自动/手动选择开关打到手动位置。用油缸的前进/后退按键调整前夹头的位置,准备安装试样。
4.选择适当的负荷档位,在负荷传感器不受力时,对负荷调零。注意,当连接有试样时,不可对负荷清零。
5.连接试样,准备开始试验。
6.把逻辑控制单元的自动/手动选择开关打到自动位置,调整测控单元的夹头速度按钮,选择一个适当的夹头速度,按点升/点降按钮,把试样预拉紧。
7.对位移清零,这时不可对负荷清零。
8.填写试样的截面参数,以便能有效的求得截面面积,填写试样的标距与试样长度,以便能有效的计算应变值。选择控制方式,选择适当的试验速度。按拉伸按钮,试验开始。
9.试验结束后(试验结束有两种方法,一是按下停止按钮,二是选择试样断裂保护,当试样拉断时,试验自动结束),首先保存试验数据。
10.试验结束后,可以对试验的各项参数计算和打印报表。
11.退出应用程序,关闭油泵,关闭电源。
附录D 球铰式引伸仪
材料力学实验中,除测定试件或构件的承重能力之外,往往还要测定它们的变形(如测定材料的弹性模量时)。变形一般很小,要用高精度、高放大倍数的仪器才能测出,这类仪器即为变形仪。变形仪的种类很多,球铰式引伸仪是机械式引伸仪的一种。
安装于试件上的引伸仪,只能感受试件上长为
的一段的变形。
称为标距,引伸仪测出的是
的长度变化即总变形
,由此算出的应变
,其实是
范围内的平均应变。由于引伸仪上的读数
是经放大系统放大后的数值,应除以引伸仪的放大系数k才是实际的变形
,即
。仪器能测量的最大范围称为量程。量程、标距和放大倍数是引伸仪的主要参数。
一、百分表和千分表
百分表和千分表是广泛用来测量小变形的机械式仪表,如图D-1所示。工作时将细轴的触头紧靠在被测量的物体上,物体的变形将引起触头的上下移动,细轴上的平齿便推动小齿轮以及它同轴的大齿轮转动,大齿轮带动指针齿轮,于是大指针相随转动。如大指针在刻度盘上每转动一格,表示触头的位移为1/1000㎜,则放大倍数为1000,称为千分表。如大指针在刻度盘上每转动一格,表示触头的位移为1/100㎜,则称为百分表。大指针转动的圈数可由量程指针予以记忆。百分表的量程一般为5~10㎜,千分表的量程则为3㎜。

二、球铰式引伸仪
图D-2为球铰式引伸仪的结构和安装示意图。上、下标距叉由球铰杆和表座板(也是标距板)连接起来,并用弹簧拉紧,组成变形传递架。装于表座板上的百分表的触头与下标距叉接触。旋紧固定顶尖和活动顶尖便可把引伸仪安装于试件上。试件变形时,上标距叉基本不动,下标距叉则因活动顶尖位移,绕球铰中心轻微转动。这样,下标距叉形成一个以球铰为支点的杠杆。按照图D-2(a)所表示的几何尺寸,百分表触头的位移是活动顶尖位移(即试件变形)的两倍。即百分表指针每转动一格,表示触头的位移是1/100㎜,而试件的变形为1/200㎜。
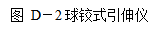
三、安装球铰式引伸仪的注意事项:
1.根据试件的尺寸调整定位块和顶尖。使小轴的尾部向上,限制上、下标距叉相对错动。把引伸仪套在试件上,使定位块与试件紧靠,旋紧活动顶尖,使顶尖嵌入试件约为0.05~0.1㎜。
2.调整接触螺钉,使百分表的量程指针指在量程的一半左右。用锁紧螺母锁紧接触螺钉。把百分表大指针调整到零位。把小轴尾部旋转向下,即可开始试验。
附录E 组合式材料力学多功能实验台
组合式材料力学多功能实验台是方便同学们自己动手作材料力学电测实验的设备,一个实验台可做七个以上电测实验,功能全面,操作简单。
一、 构造及工作原理
1.外形结构
实验台为框架式结构,分前后两片架,其外形结构如图E-1。前片架可做弯扭组合受力分析,材料弹性模量、泊松比测定,偏心拉伸实验,压杆稳定实验,悬臂梁实验、等强度梁实验;后片架可做纯弯曲梁正应力实验,电阻应变片灵敏系数标定,组合叠梁实验等。
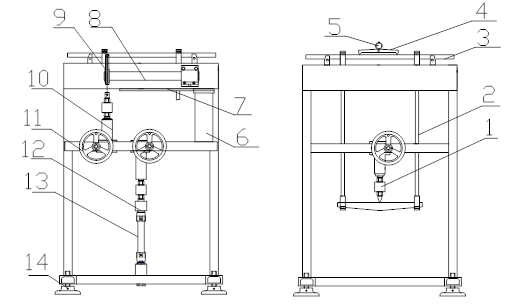
前面 后面
图E-1 组合式材料力学多功能实验台外形结构图
1.传感器; 2.弯曲梁附件; 3.弯曲梁; 4.三点挠度仪;
5.千分表(用户需另配); 6.悬臂梁附件; 7.悬臂梁;
8.扭转筒; 9.扭转附件; 10.加载机构; 11.手轮;
12.拉伸附件; 13.拉伸试件; 14.可调节底盘
2.加载原理
加载机构为内置式,采用蜗轮蜗杆及螺旋传动的原理,在不产生对轮齿破坏的情况下,对试件进行施力加载,该设计采用了两种省力机械机构组合在一起,将手轮的转动变成了螺旋千斤加载的直线运动,具有操作省力,加载稳定等特点。
3.工作机理
实验台采用蜗杆和螺旋复合加载机构,通过传感器及过渡加载附件对试件进行施力加载,加载力大小经拉压力传感器由力&应变综合参数测试仪的测力部分测出所施加的力值;各试件的受力变形,通过力&应变综合参数测试仪的测试应变部分显示出来,该测试设备备有微机接口,所有数据可由计算机分析处理打印。
二、 操作步骤
1. 将所作实验的试件通过有关附件连接到架体相应位置,连接拉
压力传感器和加载件到加载机构上去。
2. 连接传感器电缆线到仪器传感器输入插座,连接应变片导线到仪器的各个通道接口上去。
3. 打开仪器电源,预热约20分钟左右,输入传感器量程及灵敏度和应变片灵敏系数(一般首次使用时已调好,如实验项目及传感器没有改变,可不必重新设置),在不加载的情况下将测力量和应变量调至零。
4. 在初始值以上对各试件进行分级加载,转动手轮速度要均匀,记下各级力值和试件产生的应变值进行计算、分析和验证,如已与微机连接,则全部数据可由计算机进行简单的分析并打印。
三、 注意事项
1. 每次实验最好先将试件摆放好,仪器接通电源,打开仪器预热约20分钟左右,讲完课再作实验。
2. 各项实验不得超过规定的终载的最大拉压力。
3. 加载机构作用行程为50mm,手轮转动快到行程末端时应缓慢转动,以免撞坏有关定位件。
4. 所有实验进行完后,应释放加力机构,最好拆下试件,以免闲杂人员乱动损坏传感器和有关试件。
5. 蜗杆加载机构每半年或定期加润滑机油,避免干磨损,缩短使用寿命。
§E-2 电测法的基本原理
电测法的基本原理是用电阻应变片测定构件表面的线应变,再根据应变—应力关系确定构件表面应力状态的一种实验应力分析方法。这种方法是将电阻应变片粘贴的被测构件表面,当构件变形时,电阻应变片的电阻值将发生相应的变化,然后通过电阻应变仪将此电阻变化转换成电压(或电流)的变化,再换算成应变值或者输出与此应变成正比的电压(或电流)的信号,由记录仪进行记录,就可得到所测定的应变或应力。其原理框图如图E-2。


敏 感 元 件 测 量 仪 器

光、电、机传感器 数据采集与处理















图E-2 电测技术原理图
电测法的优点:
(1)测量灵敏度和精度高。其最小应变为1με(με—微应变,1με=10-6ε)。在常温静态测量时,误差一般为1~3%;动态测量时,误差在3~5%范围内。
(2)测量范围广。可测±1~2×104με;力或重力的测量范围10-2~
105N等。
(3)频率响应好。可以测量从静态到数105Hz动态应变。
(4)轻便灵活。在现场或野外等恶劣环境下均可进行测试。
(5)能在高、低温或高压环境等特殊条件下进行测量。
(6)便于与计算机联结进行数据采集与处理,易于实现数字化、自动化及无线电遥测。
电测法测量电路及其工作原理
1. 电桥基本特性
通过电阻应变片可以将试件的应变转换成应变片的电阻变化,通常这
种电阻变化很小。测量电路的作用就是将电阻应变片感受到的电阻变化率
△R/R变换成电压(或电流)信号,再经过放大器将信号放大、输出。
测量电路有多种,惠斯登电路是最常用的电路,如图2-3。设电桥各桥臂电阻分别为R1、R2、R3、R4,其中任一桥臂都可以是电阻应变片。电桥的A、C为输入端接电源E,B、D为输出端,输出电压为UBD。
从ABC半个电桥来看,A、C间的电压为E,流经R1的电流为
I1=E /(R1+R2)
R1
两端的电压降为 B

R1 R2

UAB=I1R1=R1E/(R1+R2)
UBD



同理,R3两端的电压降为 A C

UAD=I3R3=R3E/(R3+R4) R3 R4
D

因此可得到电桥输出电压为 E
图E-3
UBD= UAB- UAD= R1E/(R1+R2)- R3E/(R3+R4)= (R1R4-R2R3)E/(R1+R2)(R3+R4)
由上式可知,当
R1R4=R2R3 或 R1/R2=R3/R4
时,输出电压UBD为零,成为电桥平衡。
设电桥的四个桥臂与粘在构件上的四枚电阻应变片联接,当构件变形时,其电阻值的变化分别为:R1+△R1 、R2+△R2、R3+△R3 、R4+△R4 ,此时电桥的输出电压为

UBD=E
经整理、简化并略去高阶小量,可得

UBD=E (△R1 /R1 -△R2/ R2-△R3 / R3+△R4 / R4)
当四个桥臂电阻值均相等时即:R1=R2=R3=R4=R,且它们的灵敏系数均相同,则将关系式 △R/R=Kε带入上式,则有电桥输出电压为

UBD = (△R1 /R1 -△R2/ R2-△R3 / R3+△R4 / R4)

= V(ε1 -ε2-ε3+ε4) (E-1)
由于电阻应变片是测量应变的专用仪器,电阻应变仪的输出电压UBD是用应变值εd直接显示的。电阻应变仪有一个灵敏系数K0,在测量应变时,只需将电阻应变仪的灵敏系数调节到与应变片的灵敏系数相等。则εd =ε,即应变仪的读数应变εd 值不需进行修正,否则,需按下式进行修正
K0εd =Kε (E-2)
则其输出电压为




UBD= = (ε1 -ε2-ε3+ε4)= εd
由此可得电阻应变仪的读数应变为

εd = = =ε1 -ε2-ε3+ε4 (E-3)
式中ε1 、ε2、ε3、ε4 分别为R1、R2、R3、R4感受的应变值。
上式表明电桥的输出电压与各桥臂应变的代数和成正比。应变ε的符号由变形方向决定,一般规定拉应变为正,压应变为负。由上式可知,电桥具有以下基本特性:两相邻桥臂电阻所感受的应变ε代数值相减;而两相对桥臂电阻所感受的应变ε代数值相加。这种作用也称为电桥的加减性。利用电桥的这一特性,正确地布片和组桥,可以提高测量的灵敏度、减少误差、测取某一应变分量和补偿温度影响。
2. 温度补偿
电阻应变片对温度变化十分敏感。当环境温度变化时,因应变片的线膨胀系数与被测构件的线膨胀系数不同,且敏感栅的电阻值随温度的变化而变化,所以测得应变将包含温度变化的影响,不能反映构件的实际应变,因此在测量中必须设法消除温度变化的影响。
消除温度影响的措施是温度补偿。在常温应变测量中温度补偿的方法是采用桥路补偿法。它是利用电桥特性进行温度补偿的。
(1)补偿块补偿法
把粘贴在构件被测点处的应变片称为工作片,接入电桥的AB桥臂;另外以相同规格的应变片粘贴在与被测构件相同材料但不参与变形的一块材料上,并与被测构件处于相同温度条件下,称为温度补偿片,将它接入电桥与工作片组成测量电桥的半桥,电桥的另外两桥臂为应变仪内部固定无感标准电阻,组成等臂电桥。有电桥特性可知,只要将补偿片正确的接在桥路中即可消除温度变化所产生的影响。
(2)工作片补偿法
这种方法不需要补偿片和补偿块,而是在同一被测构件上粘贴几个工作应变片,根据电桥的基本特性及构件的受力情况,将工作片正确地接入电桥中,即可消除温度变化所引起的应变,得到所需测量的应变。
3. 应变片在电桥中的接线方法
应变片在测量电桥中,利用电桥的基本特性,可用各种不同的接线方
法以达到温度补偿;从复杂的变形中测出所需要的应变分量;提高测量灵敏度和减少误差。
(1) 半桥接线方法
①单臂测量(图E-4a):电桥中只有一个桥臂接工作应变片(常用AB桥臂),而另一桥臂接温度补偿片(常用BC桥臂),CD和DA桥臂接应变仪内标准电阻。考虑温度引起的电阻变化,按公式(E-3)可得到应变仪的读数应变为
εd =ε1+ε1t-ε2t
由于R1 和R2温度条件完全相同,因此(△R1 / R1)t=(△R2 / R2)t,所以电桥的输出电压只与工作片引起的电阻变化有关,与温度变化无关,即应变仪的读数为
εd =ε1
②半桥测量(图E-4b):电桥的两个桥臂AB和BC上均接工作应变片,CD和DA两个桥臂接应变仪内标准电阻。两工作应变片处在相同温度条件下,(△R1 / R1)t=(△R2 / R2)t,所以应变仪的读数为
εd =(ε1+ε1t)―(ε2+ε2t)=ε1―ε2
由桥路的基本特性,自动消除了温度的影响,无需另接温度补偿片。



B B
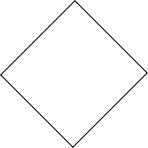
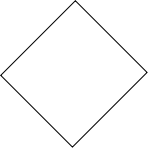
R1 R R1 R2


dUDB dUDB





A C A C



R3 R4 R3 R4

D D
E E



(a)半桥单臂测量 (b)半桥测量
图E-4 半桥电路接线法
(2) 全桥接线法
①对臂测量(图E-4c):电桥中相对的两个桥臂接工作片(常用AB和CD桥臂),另两个桥臂接温度补偿片。此时,四个桥臂的电阻处于相同的温度条件下,相互抵消了温度的影响。应变仪的读数为
εd =(ε1+ε1t)―ε2t-ε3t+(ε4+ε4t)=ε1+ε4
②全桥测量(图E-4d):电桥中的四个桥臂上全部接工作应变片,由于它们处于相同的温度条件下,相互抵消了温度的影响。应变仪的读数为
εd =ε1―ε2-ε3+ε4



B B
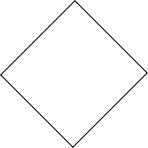
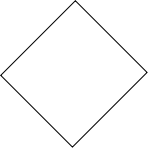
R1 R2 R1 R2


dUDB dUDB





A C A C



R3 R4 R3 R4

D D
E E



(d)相对桥臂测量 (e)全桥测量
图E-4 全桥电路接线法
(3) 桥臂系数
同一个被测量值,其组桥方式不同,应变仪的读数εd 也不相同。定
义测量出的应变仪的读数εd 与待测应变ε之比为桥臂系数,因此桥臂系数B为
B=εd /ε